Showcasing Application Cases of Viscosity-Reducing Superplasticizers for Mechanism Sand
Introduction: The Rise of Mechanism Sand and Viscosity Challenges
Mechanism sand, a crushed stone alternative to natural sand, has gained popularity due to environmental regulations and natural resource depletion. However, its irregular particle shape, high fines content, and surface roughness often lead to excessive concrete viscosity. High viscosity reduces workability, increases pumping resistance, and delays placement, posing significant challenges for contractors. This article explores how viscosity-reducing superplasticizers (VRS) address these issues through real-world application cases, highlighting their technical advantages and operational benefits.
Understanding Mechanism Sand’s Viscosity Problem
Key Contributing Factors
- Irregular Particle Morphology: Angular and rough-surfaced particles create interlocking, increasing internal friction.
- High Stone Powder Content: Fine particles (≤0.075mm) absorb more water, thickening the paste matrix.
- Surface Area Effects: Larger surface area requires more water for Wetting, leading to higher water-cement ratios if unaddressed.
Consequences in Construction
- Poor pumpability in high-rise projects
- Reduced flowability for complex formworks
- Increased energy consumption during mixing
- Higher labor costs due to prolonged placement times
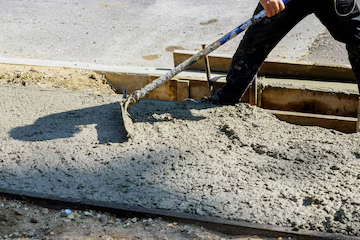
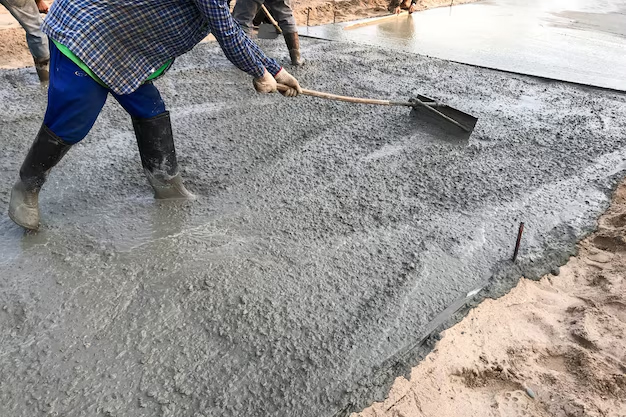
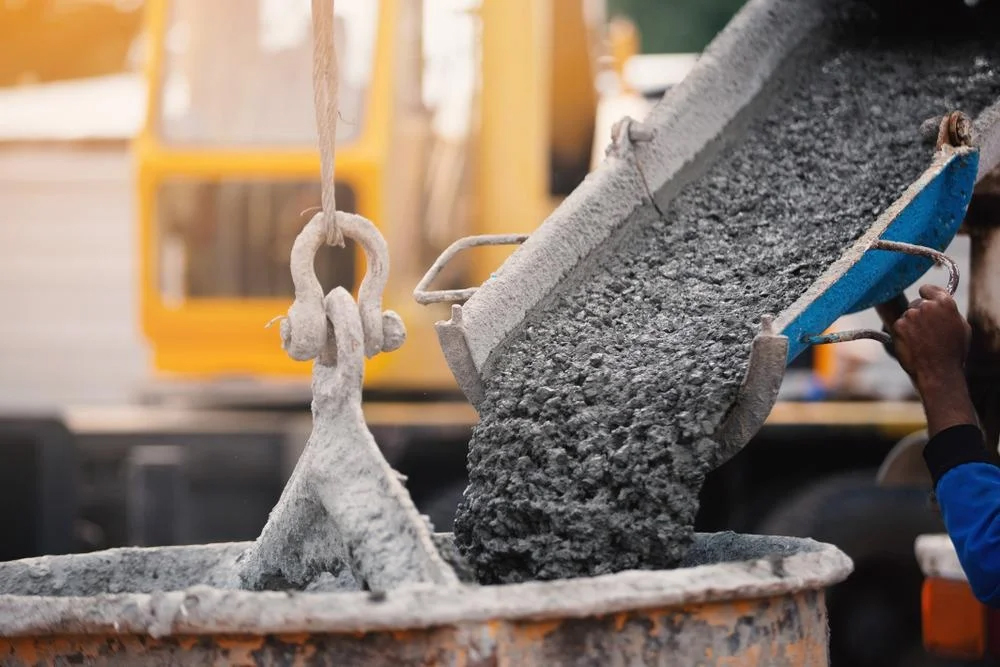
How Viscosity-Reducing Superplasticizers Work
VRS are specialized admixtures designed to:
- Enhance Particle Dispersibility: Polycarboxylate-based VRS molecules adsorb onto cement and sand particles, creating electrostatic repulsion and steric hindrance.
- Optimize Water Utilization: Reduce free water demand by improving paste fluidity, maintaining workability at lower water-cement ratios.
- Mitigate Stone Powder Impact: Specific polymers neutralize fines’ water-absorbing properties, preventing paste thickening.
Case Study 1: High-Rise Construction in Southeast Asia
Project: 50-story commercial tower in Jakarta, Indonesia
Challenge: Mechanism sand with 12% stone powder caused slump loss from 200mm to 80mm within 30 minutes, making泵送 impossible.
Solution:
- Replaced conventional superplasticizer with VRS-100 (polycarboxylate-based, viscosity-reducing type)
- Dosage adjusted from 1.2% to 1.5% by cement weight
Results: - Slump retention: 180mm after 60 minutes
- Viscosity reduced by 35% (measured via Marsh funnel time: 28s → 18s)
- Pumping pressure decreased by 22%, enabling continuous placement
Expert Quote: “VRS transformed our mix design. We no longer struggle with Pipe blockage issues, even in 35°C heat.” – PT. Astra Construction, Site Manager
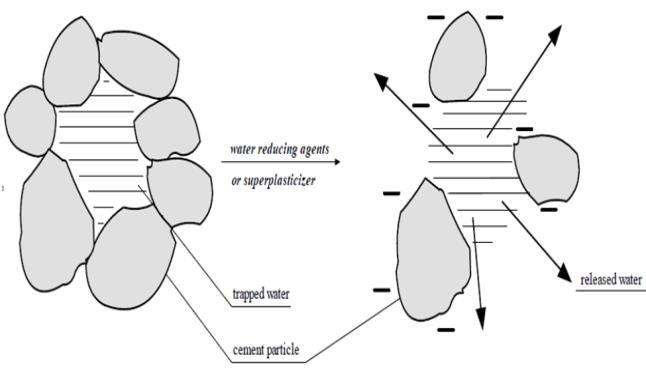
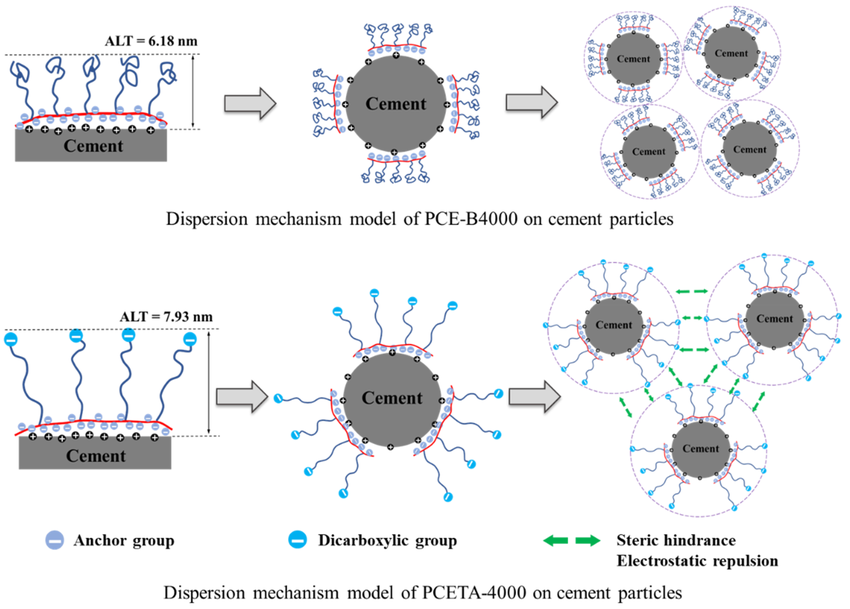
Technical Advantages of VRS in Mechanism Sand Mixes
1. Balanced Dispersibility and Retention
Unlike standard superplasticizers, VRS maintain dispersion efficiency over time, critical for long transport times or large pours.
Case Study 2: Highway Project in India
Project: 50km highway expansion in Rajasthan, using local mechanism sand (15% stone powder, high SiO₂ content)
Challenge: High alkali-silica reactivity (ASR) risks and sticky paste texture
Solution:
- Deployed VRS-200 (low-alkali, high-retention formula)
- Water-cement ratio reduced from 0.45 to 0.38 without compromising workability
Results: - 28-day compressive strength increased from 30MPa to 42MPa
- ASR expansion controlled below 0.02% (ASTM C1293 standard)
- Labor productivity improved by 18% due to faster placement
2. Adaptability to Diverse Aggregate Sources
VRS formulations can be tailored to regional mechanism sand characteristics, such as calcareous vs. siliceous aggregates.
Case Study 3: Dam Construction in Brazil
Project: Hydroelectric dam in Amazonas, using basalt-based mechanism sand (high iron content)
Challenge: High viscosity caused segregation during mass placement
Solution:
- Developed custom VRS-300 with enhanced iron ion tolerance
- Dosage optimized at 1.8% with 0.2% viscosity modifier
Results: - Segregation index reduced from 15% to 5% (ASTM C1610)
- Temperature rise during hydration controlled within design limits
- Project completed 2 weeks ahead of schedule
Real-World Benefits: Beyond Viscosity Reduction
1. Cost Efficiency
- Reduced water usage lowers cement demand
- Faster placement reduces equipment and labor hours
- Minimized waste from failed mixes
Data Insight: A Chinese study showed VRS use in mechanism sand concrete reduced overall costs by 12-15% compared to traditional mixes.
2. Environmental Sustainability
- Promotes reuse of quarry by-products (stone powder)
- Lowers carbon footprint via reduced cement consumption
- Supports circular economy goals in construction
Case Study 4: Green Building in Europe
Project: LEED-certified office complex in Berlin, using recycled concrete aggregate (RCA) with 20% mechanism sand
Solution:
- VRS-400 (bio-based polymer formulation)
- Achieved EN 206-1 compliance with 30% cement replacement by fly ash
Results: - CO₂ emissions reduced by 25% compared to conventional mixes
- Earned additional LEED credits for material sustainability
Market Trends: Growing Adoption of VRS
- Regulatory Drivers: Governments in China, India, and the EU mandate reduced natural sand extraction, pushing mechanism sand use.
- Technological Innovation: Development of AI-driven admixture dosing systems to optimize VRS performance in real time.
- Global Demand: The global superplasticizer market is projected to reach $12.8 billion by 2030, with VRS segments growing at 6.5% CAGR (Grand View Research, 2023).
Challenges and Future Directions
Current Hurdles
- Limited awareness of VRS benefits in emerging markets
- Variability in mechanism sand quality requiring site-specific testing
- Higher upfront costs compared to generic superplasticizers
Innovation Outlook
- Development of multifunctional VRS (viscosity reduction + self-healing properties)
- Bio-based polymers derived from agricultural waste
- Digital tools for real-time viscosity monitoring via IoT sensors
Conclusion: VRS as a Catalyst for Mechanism Sand Adoption
Viscosity-reducing superplasticizers have emerged as a critical solution to mechanism sand’s inherent challenges, enabling its widespread use in sustainable construction. Through targeted dispersion, water optimization, and aggregate compatibility, VRS not only enhance workability but also drive cost and environmental benefits. As global demand for eco-friendly building materials grows, VRS will play an increasingly pivotal role in transforming the concrete industry’s approach to aggregate usage.
Notre équipe technique professionnelle est disponible 24h/24 et 7j/7 pour résoudre tous les problèmes que vous pourriez rencontrer lors de l'utilisation de nos produits.Nous attendons avec impatience votre coopération !