Maintaining optimal slump in concrete is crucial for workability and structural integrity. Naphthalene superplasticizers play a key role in achieving this, but effective strategies are needed to enhance their performance. This article explores practical methods to maximize slump retention and ensure consistent concrete quality.
- Optimize Mix Proportions for Additive Efficiency
Balancing cementitious materials and aggregate ratios boosts superplasticizer effectiveness. Start by testing different cement-to-aggregate ratios to find the ideal balance. Adjust water-to-cement ratios slightly to maintain consistency without compromising strength. Naphthalene-based admixtures work best when combined with well-graded aggregates, so ensure proper particle size distribution.
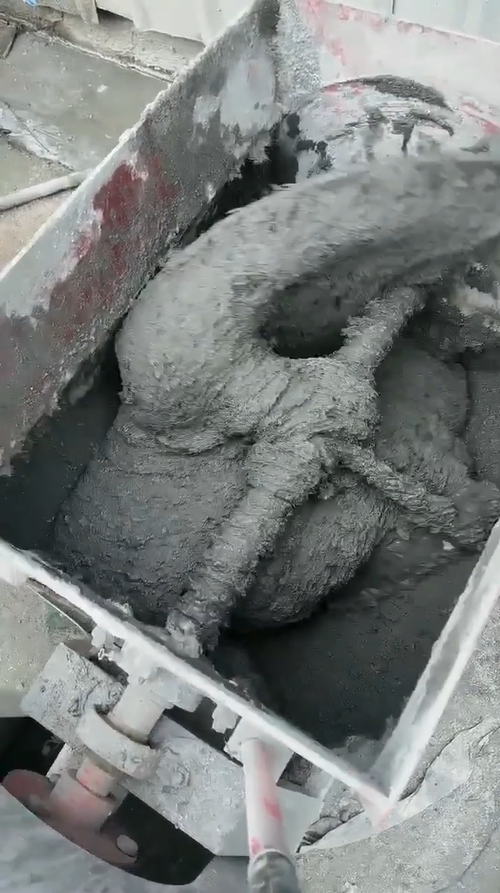
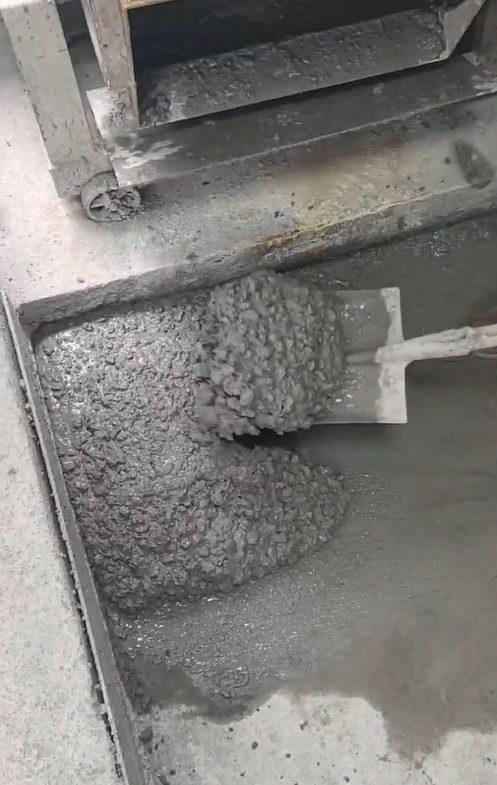

- Control Mixing and Placement Temperatures
Temperature impacts chemical reactions in concrete. High temperatures accelerate hydration, reducing slump retention. Use cooled water or ice to lower mix temperatures during hot weather. In colder conditions, warm aggregates slightly to prevent excessive heat loss. Monitor ambient temperatures throughout mixing and placement to adjust admixture dosages as needed. - Implement Proper Admixture Addition Techniques
Timing and method of adding naphthalene superplasticizers matter. Add the admixture during the final mixing stage to avoid premature dispersion. Ensure thorough mixing for 2-3 minutes to distribute the additive evenly. Pre-dissolving the superplasticizer in water can improve homogeneity, especially in large batches. Avoid over-dosing, as it may cause segregation or delayed setting. - Combine with Supplementary Cementitious Materials
Fly ash, slag, or silica fume enhance slump retention when paired with naphthalene superplasticizers. These materials improve particle packing and reduce water demand. Start with low replacement rates (10-20% for fly ash) and test slump over time. Monitor hydration rates, as some supplementary materials may slow early strength development. Balance additions to maintain both workability and long-term strength. - Adjust Batching and Delivery Processes
Efficient batching minimizes delays that reduce slump. Load aggregates first, then cement and admixtures to ensure proper coating. Use transit mixers with consistent rotation speeds to prevent segregation during transport. Plan delivery routes to reduce travel time, especially for long-distance projects. Perform slump tests immediately before placement to confirm workability and make last-minute adjustments if needed.

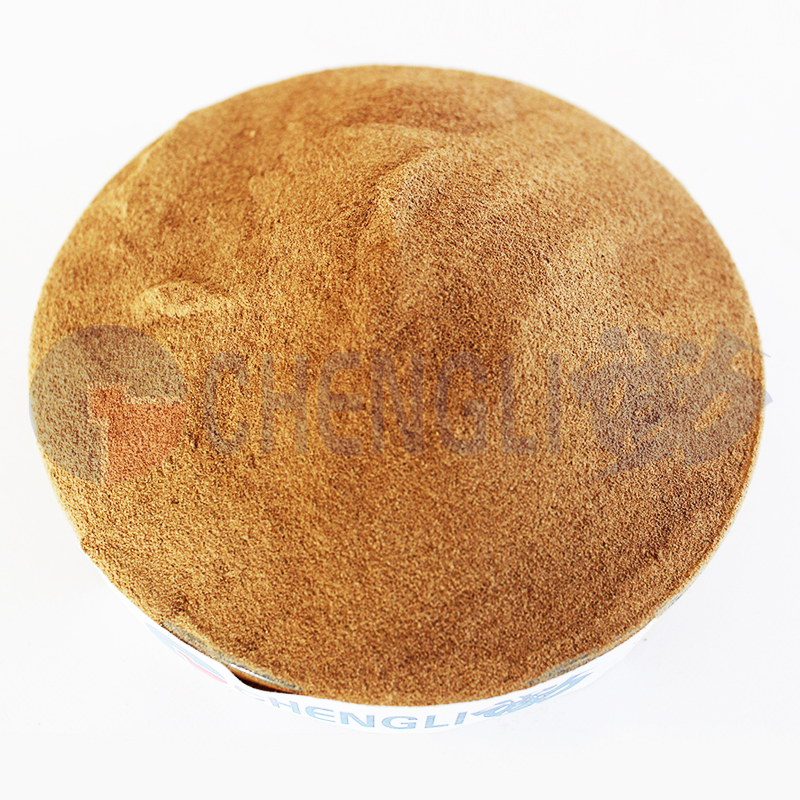
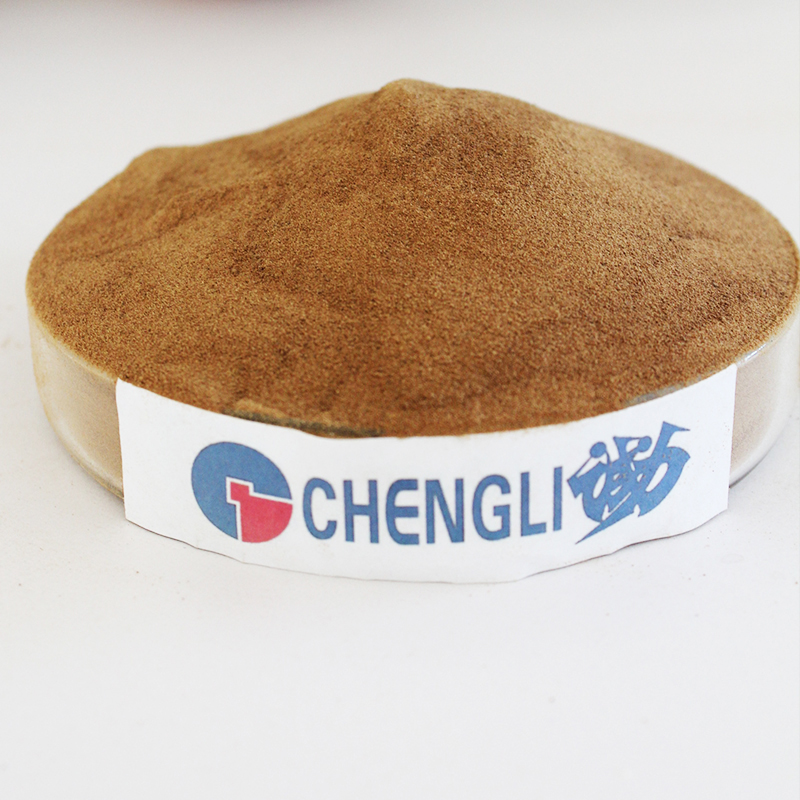
- Conduct Regular Performance Monitoring
Continuous testing ensures strategies remain effective. Perform slump tests at mixing, delivery, and placement stages. Record data on temperature, admixture dosage, and slump loss over time. Identify trends in slump retention to refine mix designs or adjust practices. Regularly calibrate mixing equipment and verify admixture concentrations to maintain consistency.
By integrating these strategies, construction teams can maximize the benefits of naphthalene superplasticizers. Proper mix design, temperature management, and admixture techniques enhance slump retention, improving workability and reducing waste. Consistent monitoring and adjustment ensure concrete meets project specifications, even in challenging conditions. Prioritizing these methods leads to more efficient workflows and higher-quality structural outcomes.
Ny Ekipa Ara-teknika Matihaninay dia azo atao 24/7 hamahana ny olana rehetra mety hatrehinao rehefa mampiasa ny vokatray. Manantena ny fiaraha-miasanao izahay!